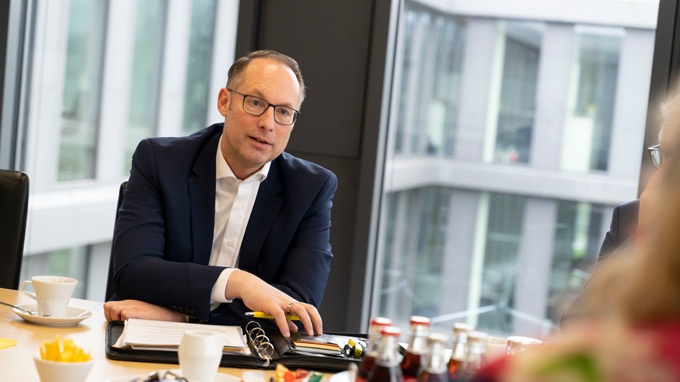
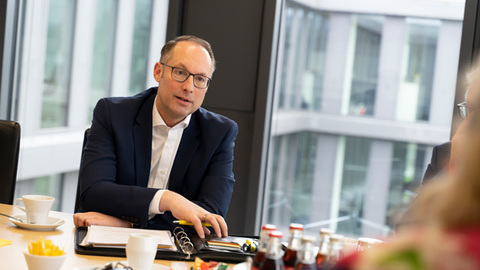
Christian Wolf sieht Turck gut gerüstet für die Herausforderungen dieser Zeit
Digitalisierung und Automatisierung sind die Brücken zur Nachhaltigkeit
Trotz der Risiken und Unwägbarkeiten von Krieg, Energiekrise und gestörten Lieferketten blickt die Automatisierungsbranche auf zwei gute Jahre zurück. Im Interview mit Anja Van Bocxlaer, Chefredakteurin der Think WIOT Group, berichten Turck-Geschäftsführer Christian Wolf und Bernd Wieseler, Leiter Produktmanagement RFID, über den Boom in der Automatisierungstechnik, den Weg zur Nachhaltigkeit und die Herausforderungen, die der digitale Wandel für große Unternehmen und KMUs mit sich bringt.
Herr Wolf, welche Herausforderungen musste Turck in den vergangenen drei Krisenjahren meistern?
Christian Wolf: Die vergangenen drei Jahre waren hinsichtlich der Ressourcenknappheit, des Fachkräftemangels und der gesamten – durch Corona und Krieg bedingten – unsicheren Lage auf jeden Fall herausfordernde Jahre. Drei Jahre mit Höhen und Tiefen. In meinen über 25 Jahren bei Turck und in der Branche habe ich beispielsweise so einen Preis- und Beschaffungskampf um Bauteile wie 2021 und 2022 noch nie erlebt. Broker bestimmten viele Preise für Bauteile und Rohmaterialien, die wir in enger Zusammenarbeit mit unseren Kunden verdauen mussten.
Wie hat sich die Krise auf die Geschäftsentwicklung ausgewirkt?
Wolf: Geschäftlich haben wir in diesen Jahren genau das Gegenteil von Krise erlebt, nämlich einen Boom in der Automatisierungstechnik. 2020 ist der Umsatz im Vergleich zum Vorjahr nur leicht gefallen. 2021 verzeichneten wir in der Automatisierungstechnik ein Wachstum von 26 Prozent. 2022 waren es immerhin noch sehr gute 16 Prozent. Ein kurioser Umstand. Die Zeit der Pandemie ist tatsächlich die erfolgreichste Zeit unserer bisherigen Unternehmensgeschichte. Die Frage, wie können wir gerade in der Pandemie dem Mitarbeitermangel, der Materialknappheit und fehlenden Fertigungskapazitäten entgegenwirken, stellte sich zeitgleich zum massiv steigenden Auftragseingang.
Worin sehen Sie die Gründe für die gestiegene Nachfrage nach Automatisierungslösungen?
Wolf: Es gibt mehrere Gründe. Allgemein ausgedrückt, liegen in der Automatisierungstechnik Lösungen für zahlreiche Probleme, die uns heute beschäftigen. Konkret lauten die vier großen gesellschaftlichen und wirtschaftlichen Herausforderungen dieser Zeit: Deglobalisierung bei intensiven weltweiten Handelsverflechtungen, Dekarbonisierung und damit das Streben nach CO2-Neutralität und Energieeffizienz sowie die Transformation hin zur Elektromobilität. Die Automatisierung und Digitalisierung aller Prozesse ist die Grundvoraussetzung für jede dieser Aufgaben. Und bei all diesen Veränderungen müssen wir auch dem demografischen Wandel erfolgreich begegnen.
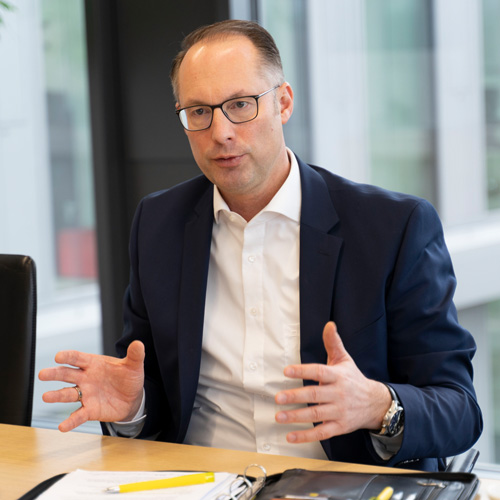
Können Sie an einem Beispiel erläutern, wie Digitalisierung und Automatisierung mit dem Thema Nachhaltigkeit zusammenhängen?
Wolf: Nehmen wir das Beispiel Maschinenbau. Ein Maschinenbauer fragt sich heute aufgrund der gestiegenen Energiepreise einerseits und der EU-Vorgaben zur Nachhaltigkeit andererseits, wie er die Produktion energieeffizienter gestalten kann. Die Antwort lautet: durch Digitalisierung und Automatisierung. Die Auswertung von Sensordaten aus Maschinen ist unerlässlich, um die Prozessgeschwindigkeiten sowie Wartungs- und Stillstandszeiten von Maschinen so einzurichten, dass die Energiebilanz optimal ist. Der Einsatz von Energie kann ebenfalls durch die Nutzung von Automatisierungstechnik optimiert werden. Die Reduzierung von Energieverbrauch und Betriebskosten sind Prozesse, die sich letztlich nur datenbasiert durch Digitalisierung lösen lassen. Insofern sind die Bestrebungen zum nachhaltigen Produzieren und Wirtschaften bedeutende Beschleuniger für die digitale Transformation in der Industrie.
Wie hat sich die Verteuerung der Energie auf die Produktion bei Turck ausgewirkt?
Wolf: Nicht so stark wie in anderen Industriebranchen, aber auch für uns sind die gestiegenen Kosten spürbar. Turck ist kein Unternehmen mit hohem Energieverbrauch. Gas nutzen wir nur in geringem Maße, und zwar nicht für Maschinen und Anlagen, sondern zum Heizen unserer Räumlichkeiten. Unsere Maschinen und Anlagen werden elektrisch betrieben. Wir haben daher Initiativen und Investitionen gestartet, um den Anteil der Photovoltaik an unserer Energieversorgung zeitnah deutlich zu erhöhen. Damit wollen wir deutlich stärker zum energetischen Selbstversorger werden. Ich begrüße es generell, dass in Energiefragen ein ökologisches Umdenken in der Industrie stattfindet, um in der Zukunft unabhängiger von Gaslieferungen zu werden.
Sehen Sie eine Möglichkeit, Resilienz gegen die Auswirkungen geopolitischer Krisen aufzubauen?
Wolf: Wenn man davon ausgeht, dass die wirtschaftliche Entwicklung volatil bleibt, muss man sich auf der Kapazitätsseite breiter aufstellen, um bei einer stark ansteigenden Nachfrage schnell auf die Anforderungen der Kunden zu reagieren. Denn eine hohe Verfügbarkeit wird auch zukünftig ein entscheidendes Kriterium für den wirtschaftlichen Erfolg von Unternehmen bilden. Letztlich heißt dies antizyklisch zu agieren.
Es wird also auch zukünftig immer häufiger zu einer Abkühlung des Wirtschaftsklimas nach drei bis vier Jahren kommen. Um trotzdem längerfristig planen zu können, arbeiten wir bei Turck jetzt an einer strukturierten Fünfjahresplanung. Die Unsicherheiten durch geopolitische Spannungen müssen wir als Unternehmen wieder in Unternehmertum ummünzen und auch in schlechten Zeiten auf dem Investitionspfad bleiben.
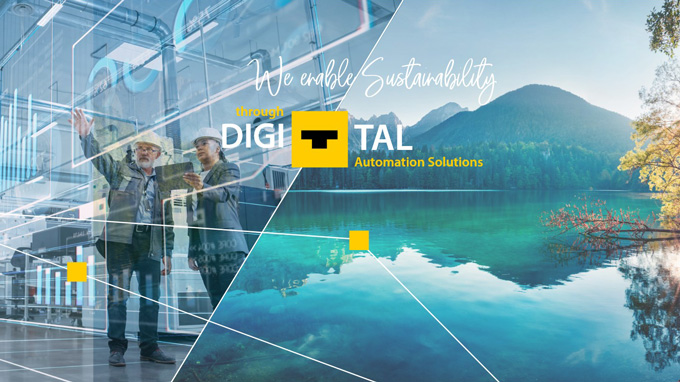
Herr Wieseler, wie ist die Produktentwicklung 2022 bei Turck verlaufen?
Bernd Wieseler: Der größte Teil unserer Entwicklungskapazität ist in das Re-Design von bestehenden Schaltungen und Layouts geflossen, um trotz fehlender oder völlig überteuerter Komponenten weiterhin lieferfähig zu bleiben. Darüber hinaus haben wir viele Firmware-Updates zur Optimierung der IIoT-Funktionalitäten unserer Lösungen entwickelt. Nehmen wir beispielsweise die RFID-Interfaces in IP67: Wir haben sie mit OPC UA um AutoID Companion Specification V. 1.01 und HF-Busmodus erweitert. Dadurch ist die reibungslose direkte Kommunikation mit MES-, SPS-, ERP- oder Cloud-Systemen möglich.
Oder der HF-Busmodus unserer RFID-Interfaces, der bei Anwendungen mit vielen Lesepunkten große Zeit- und Kostenvorteile bietet. Damit können pro Kanal bis zu 32 HF-Schreib-Lesegeräte einfach per T-Stück in Reihe geschaltet werden. Über OPC UA verbinden wir mit einfachen Methoden die Geräte und erhalten leichter Zugriff auch bei kleineren Applikationen.
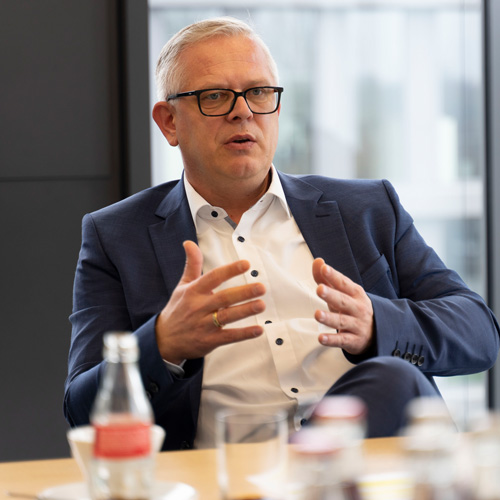
Wird Turck in Zukunft häufiger Softwareprodukte anbieten?
Wieseler: Wir setzen Software ein, um Systeme anzuschließen und dem Kunden die Verwendung unserer Produkte so einfach wie möglich zu machen. Aber wir sind in erster Linie ein Hardware-Hersteller und die Software weist immer einen direkten Bezug zu unserer Hardware auf. Mit TAS, der Turck Automation Suite beispielsweise, helfen wir unseren Kunden, so viel wie möglich aus ihren Turck-Geräten herauszuholen. Die Softwareentwicklung spielt bei unseren Produkten zwar eine enorm wichtige Rolle, bedeutet aber nicht, dass wir ein Systemhaus sind.
Können Sie TAS erklären?
Wieseler: Sehr gern. TAS ist eine IIoT-Plattform, die das Management und die Konfiguration von Turck-Geräten in industriellen Ethernet-Netzwerken vereinfacht. Mit TAS wird die Phase der Inbetriebnahme durch Visualisierung einfacher, aber durch Batch-Funktionen auch schneller, etwa bei Firmware-Updates oder der Vergabe von IP-Adressen. Wir generieren damit Mehrwert für den Kunden, weil er alle Produkte mit einer Plattform überblicken und ansprechen kann. Schon in der ersten Version hatten wir viele Beispiele und nutzbare Applikationen integriert, wie zum Beispiel Proof of Concepts mit unseren Produkten einfach bildlich darzustellen. RFID-Anwendungen und -Geräte leicht ansprechen zu können, ist ein ganz großes Thema in der Entwicklungsarbeit von TAS.
Warum war der Fokus auf einer Verbesserung im RFID-Bereich notwendig?
Wieseler: Die Einrichtung eines RFID-Gates war mit viel Aufwand verbunden. Der Kunde musste erst seine Antennen ausrichten. Anschließend herausfinden, welcher Tag erfasst wurde und wo er sich befindet. Auf dieser Basis ließen sich erste Schlussfolgerungen ziehen. Aber es war alles relativ rudimentär dargestellt. In der neuen Version stellen wir in TAS bessere Tools zur Verfügung, die die Prozesse auf den einzelnen Ebenen in so einem Gate erfassen und darstellen. Wie die Datenträger in den Ebenen gelesen werden, kann zweidimensional oder dreidimensional dargestellt werden. Diese Darstellung hilft unseren Kunden.
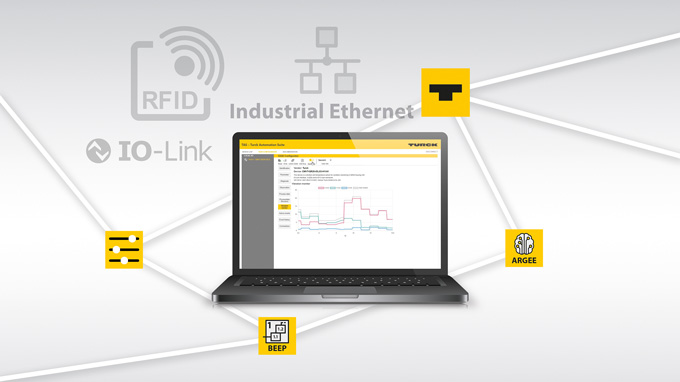
Worüber erhält der Kunde Aufschluss, wenn er Einblick in unterschiedliche Ebenen bekommt?
Wieseler: Über die Position der Tags. Wenn ich beispielsweise eine Palette mit mehreren Produkten durch das Gate bringe, sieht er, wie viele von vorne gelesen werden können, in der Mitte oder hinten. Er sieht, welche Feldstärke benötigt wird und weiß dann, wo die Antennenposition angepasst werden sollte.
Wie unterstützt TAS-Kunden dabei, Datenträger möglichst energieeffizient auszulesen?
Wieseler: Dafür haben wir ebenfalls ein neues Tool. In der Vergangenheit schlossen sich hohe Performance und niedriger Leistungsaufwand oft gegenseitig aus. Das neue Tool ermittelt in einem Auslesezyklus, den wir ‚Power Sweep‘ nennen, welche Parameter die beste Read-Performance ergeben und wie Datenträger optimal angesteuert werden.
Wie stark ist das RFIDSegment bei Turck momentan?
Wolf: Wir verzeichnen enorme Zuwächse und volle Auftragsbücher. Im Schnitt sind wir jedes Jahr um 25 und mehr Prozent im RFID-Bereich gewachsen, in den letzten zwei Jahren kumuliert um fast 75 Prozent. Vor allem in der Intralogistik hat Turck viele Neuanlagen mit RFID ausgestattet. Unsere Kapazitäten waren aber leider begrenzt und wir mussten daher Aufträge ablehnen. Gerade 2022 waren RFID-Produkte stark von Lieferschwierigkeiten und Materialknappheit, vor allem bei Chips, betroffen.
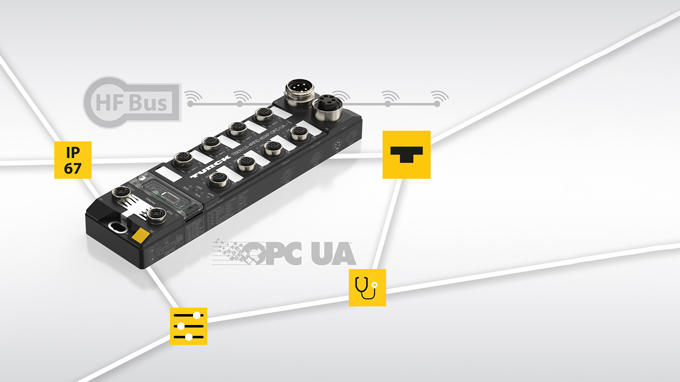
Mit Nachhaltigkeit und Digitalisierung Volldampf voraus – das hört sich nach einem Happy End an. Ist es das?
Wolf: Ja, es ergeben sich tatsächlich sehr viele Chancen aus der Digitalisierung und der Nachhaltigkeit, aber das gilt nicht für jeden Industriezweig. Energieintensive Unternehmen stehen vor großen Herausforderungen, auch wirtschaftlicher Art. Transformation bedeutet aber auch: Investieren. Beispielsweise ein Automobilzulieferer, der heute 90 Prozent des Umsatzes mit einem Getriebestrang erwirtschaftet, der im Rahmen der E-Mobilitätswende in fünf oder zehn Jahren wegfällt, muss eine Transformationsgeschwindigkeit an den Tag legen, die sehr schwer zu stemmen ist.
Was bedeutet das dann für Anbieter, die nicht ausreichend in diese Transformation investieren können?
Wolf: Für viele KMUs ist das schwer. Großunternehmen stellen teilweise ganze Mitarbeiterstäbe ab, die alle Regularien studieren und Umsetzungspläne erarbeiten. Wir bei Turck schaffen es auch noch – mit Aufwand und Investitionen. Aber beispielsweise als energieintensives Kleinunternehmen mit 50-100 Mitarbeitern bis 2030 klimaneutral zu werden und die gesamte EU-Regularien zu erfüllen, ist schon eine große Herausforderung.
Was bedeutet das für die EU und für Deutschland? KMUs stellen immerhin über 90 Prozent der Unternehmen in Deutschland.
Wolf: Ich glaube, dass das Thema ‚Nachhaltigkeit‘ für die EU ein echter Wettbewerbsvorteil sein kann. In der EU-Gesetzgebung sind jedoch Vorgaben enthalten, die bis 2030 kaum realisierbar sind. Beim Lieferkettengesetz beispielsweise wird es sehr schwer, entlang der gesamten Supply Chain bis ins kleinste Detail bei jedem Bauteil zu ermitteln, wie hoch (oder eher wie niedrig) die CO2-Emission ist. Dafür ist die Zeit zu kurz.
Sehen Sie die Position von Turck bedroht in diesem Szenario?
Wolf: Nein. Nehmen wir mal ein konkretes Beispiel wie das digitale Typenschild. Das Typenschild enthält Informationen über das Produkt und den gesamten Lebenszyklus. Unternehmen unserer Größenordnung und mit dem vorhandenen vielfältigen Kompetenzen werden das realisieren und sogar Wettbewerbsvorteile hieraus generieren. Ich glaube, die Anforderungen an ein digitales Typenschild mit einem Product Carbon Footprint, der glaubhaft belegbar ist, ist für ein KMU nur schwer umsetzbar. Dafür müssten alle Produktdaten digitalisiert werden und Lieferketten lückenlos überprüft werden.
Worauf stützen Sie Ihre Einschätzung?
Wolf: Ich bin in Mülheim ehrenamtlich im Netzwerk Zenit e.V. tätig. Zenit ist das Zentrum für Innovation und Technik in NRW, das Unternehmen eine Plattform für Vernetzung, Internationalisierung und Know-how-Transfer bietet und insbesondere auf KMUs ausgerichtet ist. Viele der kleineren und mittleren Unternehmen, mit denen ich dort in Kontakt komme, wissen teilweise noch nicht, was auf sie zukommt. Sie stehen vor einem Berg von Regularien und haben teils weder das Know-how noch die personellen Ressourcen, dies zeitgerecht umzusetzen und benötigen daher externe Unterstützung. Deswegen ist hier die Politik gefragt, differenziertere Ansätze für die Industrieunternehmen zu finden.
Autor | Das Gespräch führte Anja Van Bocxlaer, Chefredakteurin der Think WIOT Group
- Themen & Technologien