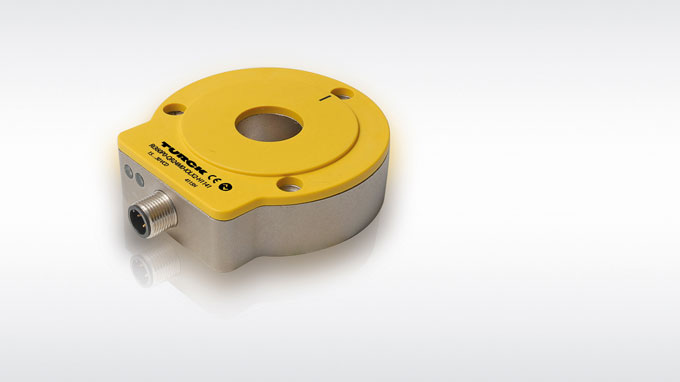
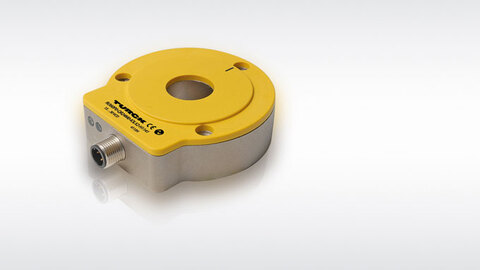
Thanks to IO-Link the QR24-IOL can be connected with inexpensive three-wire cables
First Contactless IO-Link Encoder
21/15 – QR24-IOL simplifies mounting with free zero point selection
At the SPS IPC Drives fair Turck is showcasing the first fully contactless encoder which outputs its measured value via IO-Link. This makes the QR24-IOL an inexpensive alternative to encoders with an analog interface. Users can connect the single turn encoder with a standard M12x1 male connector. Expensive shielded cables become unnecessary through the use of simple three-wire cables.
The combination with Turck's contactless measuring principle offers additional benefits. The zero point of the encoder can be selected as required – and can be set simply via IO-Link after mounting. It is thus no longer necessary to align the encoder optimally to its electrical connection and use correction factors for the zero point in the controller. The orientation of the signal (CW/CCW) can also be set via IO-Link. The absolute resolution is 0.005 degrees.
The data storage function of IO-Link 1.1 enables the plug & play exchange of the QR24 in the event of any faults. All relevant encoder parameters can be stored in the IO-Link master and are automatically used on every encoder of the same type. Even employees without any special training can thus replace the encoder reliably. The machine can continue running seamlessly without having to re-parameterize the device. The typical service requirement and associated waiting times for specialist personnel become unnecessary.
At the SPS IPC Drives fair Turck is showcasing the first fully contactless encoder which outputs its measured value via IO-Link. This makes the QR24-IOL an inexpensive alternative to encoders with an analog interface. Users can connect the single turn encoder with a standard M12x1 male connector. Expensive shielded cables become unnecessary through the use of simple three-wire cables.
The combination with Turck's contactless measuring principle offers additional benefits. The zero point of the encoder can be selected as required – and can be set simply via IO-Link after mounting. It is thus no longer necessary to align the encoder optimally to its electrical connection and use correction factors for the zero point in the controller. The the orientation of the signal (CW/CCW) can also be set via IO-Link. The absolute resolution is 0.005 degrees.
The data storage function of IO-Link 1.1 enables the plug & play exchange of the QR24 in the event of any faults. All relevant encoder parameters can be stored in the IO-Link master and are automatically used on every encoder of the same type. Even employees without any special training can thus replace the encoder reliably. The machine can continue running seamlessly without having to re-parameterize the device. The typical service requirement and associated waiting times for specialist personnel become unnecessary.