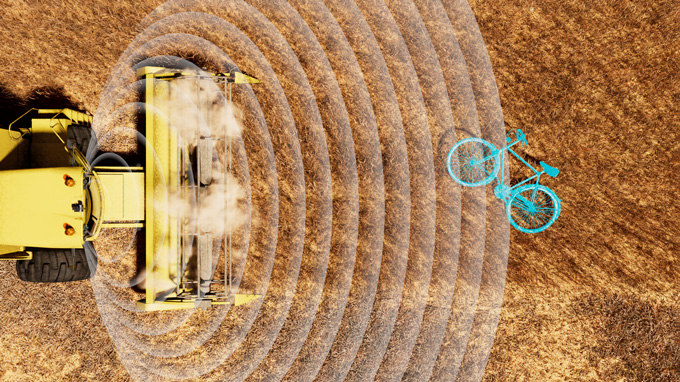
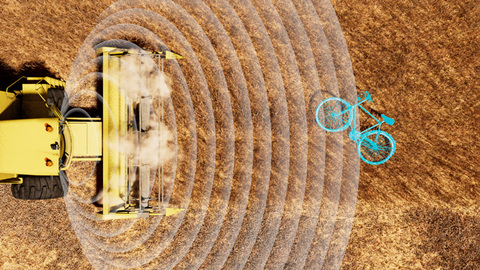
Radar Scanner Delivers 3D Data and Improves Object and Space Mapping
Turck's MR15-Q80 3D radar scanner ensures reliable object detection and collision avoidance – from mobile equipment to intralogistics
Quick Read
Many radar sensors for collision avoidance are limited to detecting the distance and thus only output one dimension as a measured value. Turck's new MR15-Q80 radar scanner, on the other hand, delivers genuine 3D data and thus significantly improves the mapping of objects and spaces, giving developers and system engineers a greater degree of freedom. Thanks to its robust design, which can withstand shocks of up to 100 g, and the SAE J1939 interface, the scanner is particularly suitable for use in mobile equipment, but also for AGVs or conventional industrial trucks in intralogistics.
We usually associate radar technology either with speed checks in road traffic or with devices for flight monitoring. But since the 2000s, the technology has also been increasingly used in cars themselves. Active adaptive cruise control (ACC) systems use radar to determine the distance to cars in front and their speed. Radars have also become increasingly popular in industrial automation in recent years. Especially in level and conventional distance measurement, the advantages over ultrasonic, optical sensor or media-contacting technologies pay off in many applications.
In 2020, Turck had already presented its first radar sensors for level measurement with the LRS series, followed by the DR-M30 radar sensors for distance measurement in 2021. Both device series operate in the 120 GHz range, which is particularly beneficial in terms of range and resolution, i.e. the accuracy of the signal. Turck is now launching the MR15-Q80 radar sensor as the third member of its radar portfolio. The shape of the housing alone shows that a new device type has been added to the product range. Unlike the cylindrical devices for distances and levels, the MR15-Q80 has a flat, cuboid design. The underlying technology is also different: A 60 gigahertz antenna operates inside the robust IP69K housing. Compared to the 120 GHz frequency band, the lower frequency provides a lower resolution, but the beam angle is significantly wider. The MR15-Q80 detects objects with an opening angle of 120 degrees horizontally and 100 degrees vertically.
The sensor achieves a range of up to a remarkable 15 meters, although this maximum value can also be reduced depending on the material, angle and surface properties of the objects. However, users do not have to worry about a lack of range as the target applications are primarily object detection and collision avoidance.
Collision control and object detection for mobile equipment
Turck's new radar scanner offers maximum IP69K protection against water and dust ingress and meets all requirements here in terms of robust component design for the mobile equipment sector. The M15-Q80 also stands out in terms of mechanical resistance, as it can withstand shocks and impacts of up to 100 g. This is where radar technology differs significantly from laser-based lidar technology. Lidar systems require movable mirrors to direct the laser beams into every corner of the area to be scanned. These moving mirrors are naturally susceptible to mechanical damage caused by impact and vibration.
Radars are therefore not only less sensitive to interference factors such as dust, fog or light reflections, but are also much more robust mechanically. Besides its resistance to severe shocks, the MR15-Q80 can also withstand supply voltages of 12 or 24 volts, which are used in the vehicle electrical systems of mobile equipment – the sensor can also withstand possible voltage peaks without damage. Turck is positioning the MR15-Q80 as a sensor for collision avoidance and object detection for all non-safety related tasks. It detects objects in its surroundings and – unlike comparable devices – outputs measured values for all three dimensions. For mobile equipment, the new radar scanner is currently the only device on the market that can output a three-dimensional measurement via the SAE J1993 communication protocol for the CAN bus.
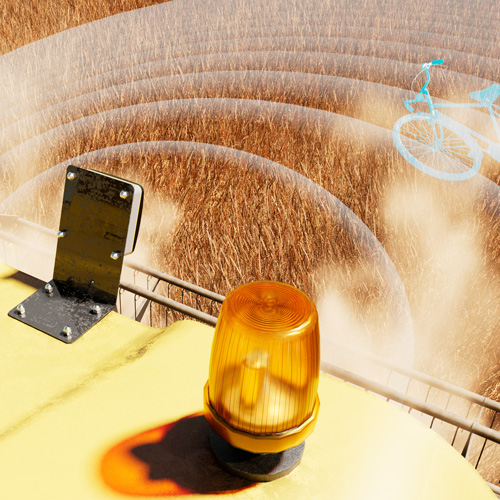
Realistic space mapping thanks to 3D data
The MR15-Q80 provides distance and speed values for objects on all three spatial axes. This means that the surroundings and all the objects in them can be depicted much more precisely. Machines in particular with arms or booms at different heights receive valuable additional information about their surroundings. Thanks to the 3D information, the control system not only knows where an obstacle begins, but also where it ends and where the machine can operate with its arms. There are many other application areas where precise knowledge of the space in front of machines can be helpful, for example when recording topography and rocky outcrops in mining.
Identifying animals and objects in the field
Another application in the mobile equipment sector is the detection of animals and objects in fields. Turck's radar scanner can be mounted on the combine harvester directly on the threshing unit to monitor the field in front of it. Due to the different reflective properties of animals or objects and grain stalks, the sensor can detect foreign objects in the field that would either get damaged themselves or could damage the threshing unit. Thanks to the large opening angles of 120 degrees horizontally and 100 degrees vertically and a range of up to 15 meters, the radar scanner can reliably detect whether the field in front of the combine harvester can be harvested without any problems.
Expert Talk: MR15-Q80
Technical Trainer Jörg Tauert and Raphael Penning, Product Manager Distance Sensors, talk about the functions and possible applications of the MR15-Q80 3D radar sensor
Walk & Talk: MR15-Q80
Get a quick overview of features and benefits from our product expert
Six adjustable warning radii and three signal spaces
For these and other applications, users can define warning radii that trigger a switching signal as soon as an object is located within them. Switching signals can also be reliably triggered by certain intensity thresholds, which are important for distinguishing objects. However, the controller can also fully evaluate the IO-Link signal in order to utilize the entire information density. Up to six freely definable warning fields and three three-dimensional signal spaces can be taught and linked to one of the two switching outputs. If one of these warning fields is in the radar shadow because there is an object between the sensor and the field, the sensor also recognizes this and outputs an appropriate message.
Another possible application on mobile equipment is blind spot warning, i.e. the monitoring of areas on the machine that are difficult to see. The vehicle may be damaged if there are any objects located there. The warning radii and signal spaces are also helpful for these tasks in order to output warning signals in good time.
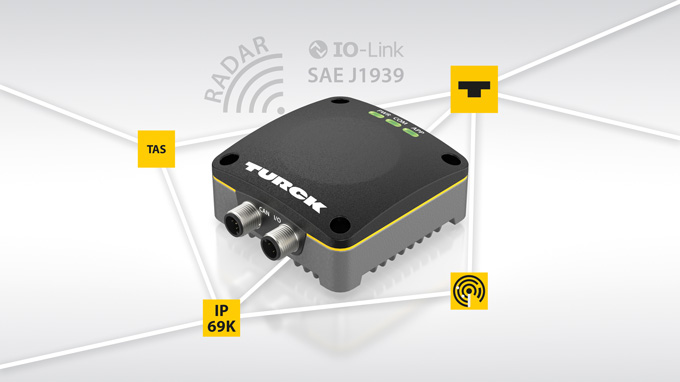
Collision avoidance in intralogistics
Alternative application fields are also emerging in intralogistics. Industrial trucks and automated guided vehicles (AGVs) in particular require sensor technology to navigate and avoid collisions. LIDAR scanners are normally used for safety-oriented environment monitoring. However, they are only suitable for the vertical monitoring of lift paths on autonomous forklift trucks to a limited extent, as they usually detect a small vertical opening angle. Special safety radars and scanners would also be oversized and therefore too expensive for the non-safety relevant function of height control.
Height control
Turck's 3D radar scanner provides the necessary information for all three spatial dimensions and thus detects obstacles and surroundings in their entirety. This information also facilitates the precise and safe control of lifting movements. The scanned data can also be used to ensure clearance heights and prevent damage to vehicles, goods and plant elements. Camera systems are often used for these tasks, but they are more expensive and usually much more complex to set up.
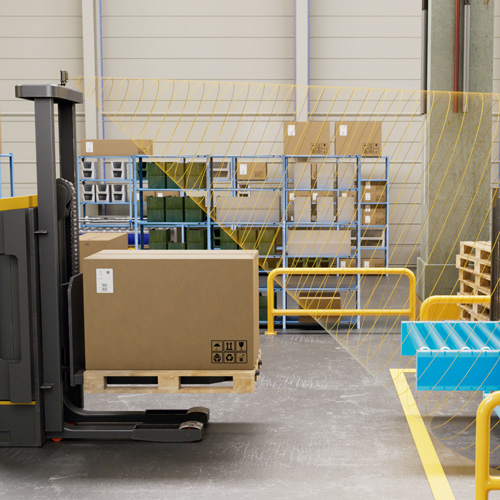
Simplified commissioning and real-time visualization in TAS
The parameterization of such complex sensors, which output more than just an analog signal or one or two switching signals, is often a challenge. Turck supports users with its TAS (Turck Automation Suite) configuration and IIoT software. The toolkit makes commissioning and optimum setting of signal and intensity filters, detection angles or warning radii much easier. The software visualizes all raw data from the sensor in virtual real time in the web browser. Objects are displayed as points and point clouds on two graphs, one for the vertical data and one for the horizontal detection angles.
Turck offers two variants of the 3D radar scanner: one with IO-Link and one with an SAE-J1939 interface, which is primarily used for mobile equipment. Besides the interface for the 3D data, both devices have two classic switching outputs that can be triggered by different threshold values.
Author: Raphael Penning is product manager for distance sensors at Turck
- Topics & Technologies