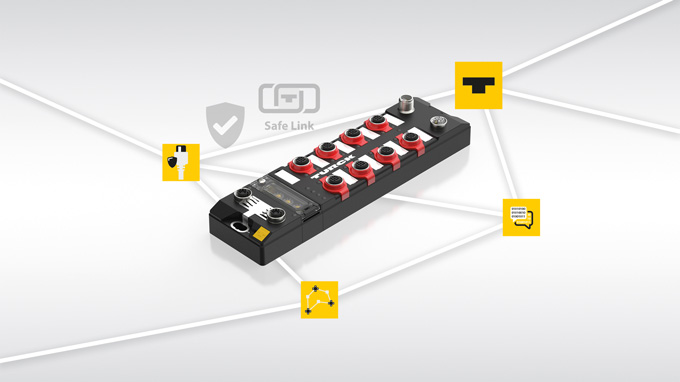
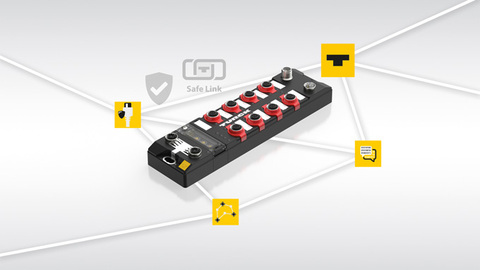
Modular Safety Network Thanks to Turck Safe Link
Turck’s networked safety platform based on the Safe Link protocol and the Ethernet multiprotocol safety I/O modules allows efficient and flexible safety solutions for small to medium-sized plants – right through to ATEX Zone 2/22
Quick Read
Turck’s Safe Link and the TBEN-LL-4FDI-4FDX Ethernet multiprotocol safety I/O modules offer an efficient and flexible solution for machine safety, particularly for small to medium-sized plants. Thanks to the Ethernet multiprotocol, the decentralized installation of the IP67 modules and the ability to network up to 31 modules with Safe Link, it is possible to create an easily scalable and modular safety network without the need for control cabinets. This solution reduces cabling effort and simplifies the installation – the ATEX approval also allows use in Zone 2/22 hazardous areas.
Machine safety plays a central role in modern industrial environments and encompasses a wide range of technologies and measures aimed at preventing accidents and injuries. In an increasingly complex industrial land-scape, it is crucial that safety devices do not work in isolation but are integrated and networked with each other. For example, a safety light curtain can stop a production line immediately if an employee enters a danger zone, while at the same time bringing nearby machines to a standstill by activating an emergency stop system. This coordinated communication between the safety components creates a comprehensive safety network that not only ensures the safety of employees, but also maximizes machine uptime.
This means in practice that an operator working on a punching machine, for example, can rely on the fact that when the safety curtain is triggered, not only the machine itself but also all conveyor belts and feed systems in the entire area are stopped immediately. This integrated reaction not only prevents injuries but also minimizes the risk of machine damage through the sudden stopping of isolated parts of the system. Another example is a robot arm in a production line: If a safety laser detects that an employee is moving too close to the robot’s working area, not only is the robot stopped, but also all the machines interacting with the robot. This ensures that the entire area is safe and that no isolated part of the system continues to run in an uncontrolled way.
Safety in small to medium-sized systems
The increasing complexity of industrial environments calls for advanced safety solutions that do not work in isolation but are integrated and networked. Particularly in small to medium-sized systems with a moderate number of safety applications, users are often confronted with specific challenges. Another critical point is the lack of flexibility of conventional solutions in dynamic production environments. Production lines that are regularly retooled require scalable safety solutions. Traditional central safety PLC systems are often oversized for the applications mentioned and involve high acquisition and operating costs. Added to this are the considerable cabling costs and the complexity of installing central systems. Adaptions to changing production requirements or system expansions are often difficult to implement with central safety solutions and are usually very expensive.
Coordinated safety measures through networking
Thanks to the Safe Link protocol, Turck’s TBEN-LL-4FDI-4FDX multiprotocol safety I/O modules can communicate safely with each other and with other devices in the network. This networking enables a coordinated response to safety-critical events throughout the entire production line. For example, a module that receives an emergency stop signal can immediately forward this information to all other modules so that all affected machines are stopped immediately. This not only ensures the safety of employees, but also minimizes the risk of machine damage and production downtime. The ability for real-time communication between the modules ensures that the safety measures are always synchronized, particularly fast and therefore efficient.
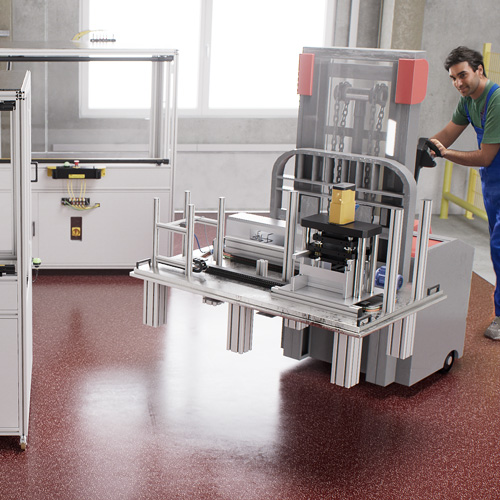
Decentralized installation for maximum flexibility and efficiency
The decentralized installation of the TBEN safety modules offers decisive advantages, especially in smaller production lines where space and cabling are often a problem. The IP67 modules can be installed directly at the machines where the safety functions are required. This reduces the need for central control cabinets as well as the amount of cabling, which not only simplifies installation, but also the maintenance and expansion of the systems. The modules offer a direct connection via M12 L-coded power supply connections and M12 D-coded Ethernet connections for reliable network communication. This means that safety-related functions can be positioned remotely directly at the source, which significantly increases the flexibility and efficiency of the production line, as short distances for safety signals allow faster cycle times.
An outstanding feature of the TBEN-LL-4FDI-4FDX multiprotocol I/O modules is their variability: Each module can be added, removed or replaced independently, enabling a rapid adaption to changing production requirements. The ability to network up to 31 modules in one application offers considerable flexibility in the design and expansion of safety solutions. Moreover, each module provides 127 diagnostic bytes for monitoring and rapid fault diagnostics, thus further increasing operational reliability. Each module is assigned two bytes of safety-related input and output data and two bytes of non-safety fieldbus bits, which can be used for communication with a non-safety PLC. The integration of one and two-channel inputs as well as safety outputs, which can be used directly to control machines and drives, allows the modules to be easily integrated into existing safety networks. This scalability enables companies to react flexibly to market requirements and technological developments without having to invest in rigid and cost-intensive safety solutions.
Expert Talk: Turck Safe Link
Walk & Talk: Turck Safe Link
Seamless integration thanks to multiprotocol
The TBEN multiprotocol safety modules support a wide range of communication protocols, including Ethernet/IP, Profinet and Modbus TCP as well as the CIP Safety and Profisafe safety protocols. This capability enables companies to maintain their existing network infrastructure and still integrate the new safety modules, thus saving time and money. This versatility makes the modules particularly attractive for companies that work in heterogeneous system landscapes and require a standardized, flexible safety solution.
Safety solutions for potentially explosive areas
For applications in hazardous areas, the multiprotocol I/O modules offer a decisive advantage thanks to their ATEX approval for Zone 2/22. The certification ensures that the safety solutions operate reliably and in accordance with legal requirements even in extreme conditions. By using these modules in potentially explosive environments, companies can ensure that their employees and systems are optimally protected, which significantly expands the possible applications and creates additional flexibility in sensitive areas.
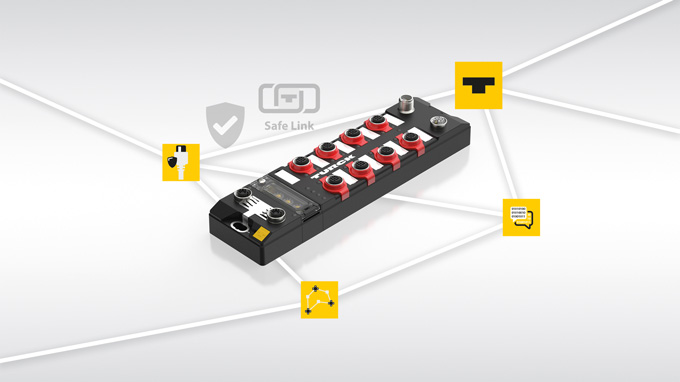
Conclusion
The integration of Turck Safe Link in the TBEN-LL-4FDI-4FDX multiprotocol safety I/O modules enables companies – especially in small to medium-sized plants – to implement a flexible, scalable and cost-efficient safety solution – up to ATEX Zone 2/22. The decentralized IP67 concept allows a tailor-made adaption to individual requirements, while the multiprotocol capability simplifies integration into existing systems. With the ability to network up to 31 modules and the integrated diagnostic functions that enable rapid fault detection, this solution offers a high level of scalability and operational reliability. The TBEN modules provide overall an efficient and economical safety platform that not only offers the highest safety standards, but also helps to maximize uptime and minimize machine damage.
Author | Michael Flesch is Product Manager Safety Systems at Turck
- Topics & Technologies