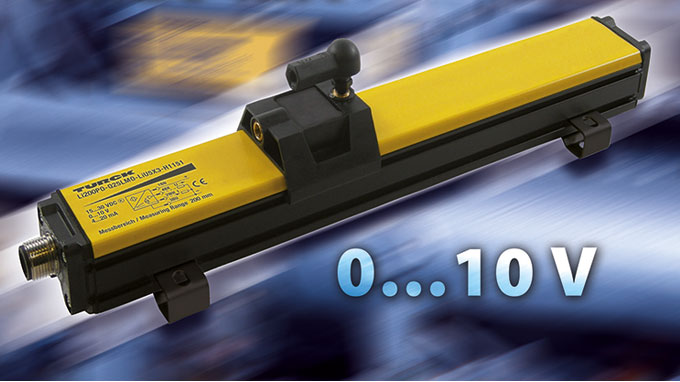
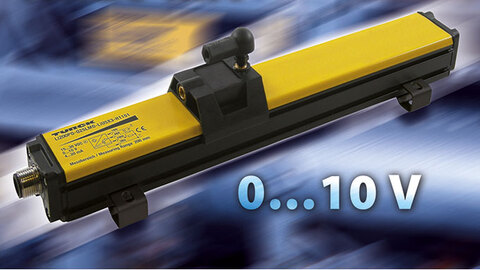
Turck's inductive LI linear position sensor is now also fit for motion control applications
Inductive Linear Position Sensors for Motion Control
23/12 – Turck is offering a high-speed inductive linear position sensor for closed-loop control tasks
Mülheim, October 2, 2012 – For the first time Turck is entering the market for high-speed motion control with its further developed LI inductive linear position sensor. A new electronics architecture increases the effective output rate of the sensor from 1 to 5 kHz. In conjunction with the short signal run time (130 µs) and the highly resolved SSi output, the inductive linear position sensors can thus achieve the performance of potentiometers but without their disadvantages. Unlike potentiometers, the LI sensors offer permanent protection to IP67, provide non-contact measuring and are absolutely wear-free. The magnetic field immune sensors are therefore suitable for measuring axes with high-speed controls such as is used in injection molding machines. Other application areas include axis measurement in packaging machines, presses or machine tools.
With the high speed and precision of the sensor (system resolution of 1 µm), machine builders can keep the position error in motor control applications to a minimum. As with all inductive linear position sensors, the high-speed variant has very short blind zones and can tolerate up to a 4 millimeter offset of the positioning element (perpendicular to the measuring axis). As well as the high-speed variant with an SSI interface and 16-bit resolution, the analog variant of the sensor will also be offered in future with the higher output rate of 5 kHz. The analog sensor has a 0…10 V or 4…20 mA output. All LI sensors continue to be available in ten measuring lengths from 100 to 1,000 millimeters. An 8-pole M12 connector is used for the connection.